
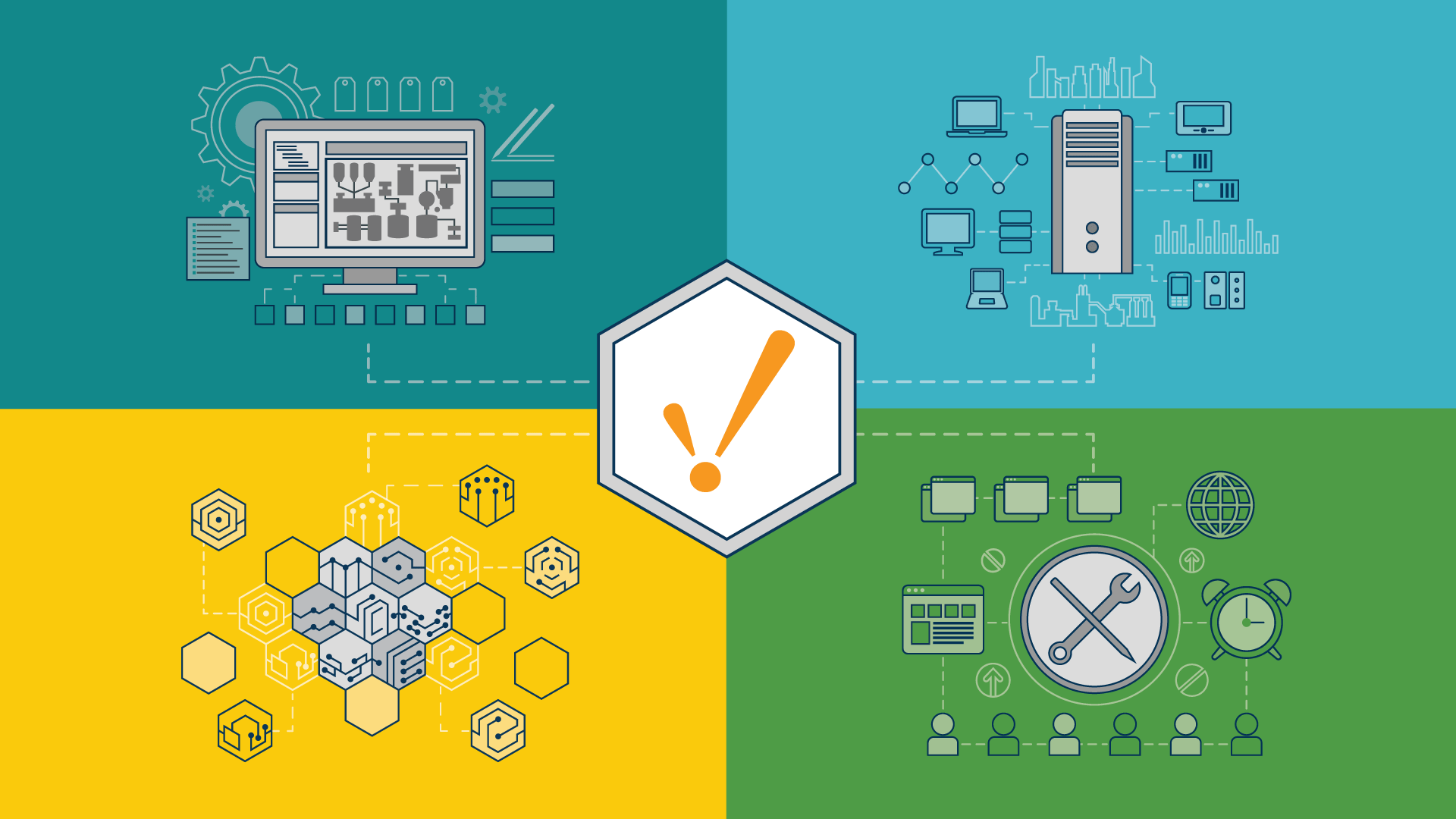
- #Inductive automation ignition preferred web service how to
- #Inductive automation ignition preferred web service software
- #Inductive automation ignition preferred web service plus
“ TwinCAT3 automation software adds programming in Visual Studio, maximized performance for multi-core PC-based controllers and IoT solutions for easy-to-implement connectivity to the cloud.” The tools are already there, and Beckhoff is working hard to implement these IoT tools in such a way that the user does not need to be an IT expert. “In the near future, we see vision and predictive maintenance functionality being implemented,” Trask adds. These features include integrated motion control, kinematics, condition monitoring, programmable safety and HMI. “This convergence of automation and IT technologies provides all the functionality needed from a PLC, while adding a wealth of other features in one programming environment,” says Bob Trask, Beckhoff Automation senior systems architect. These capabilities are provided within an architecture, often resembling a PC, and either exist on the “motherboard” itself or through the use of plug-in cards. In many respects, the PLC has evolved, and the result is a single device, the programmable automation controller (PAC), which not only handles standard logic (off/on) functions, but also can provide motion/position control, robotics supervision and process control while connecting to Ethernet networks and real-time sensor/actuator networks. The heart of any machine is its controller(s), which used to be the PLC. PLC or PAC: Does it really matter what it’s called? Moreover, the Weihenstephan Standards give recommendations for the data evaluation (e.g., traceability, calculation of efficiency identification numbers, technical reporting) and for the approval and the safe operation of MES implementations.
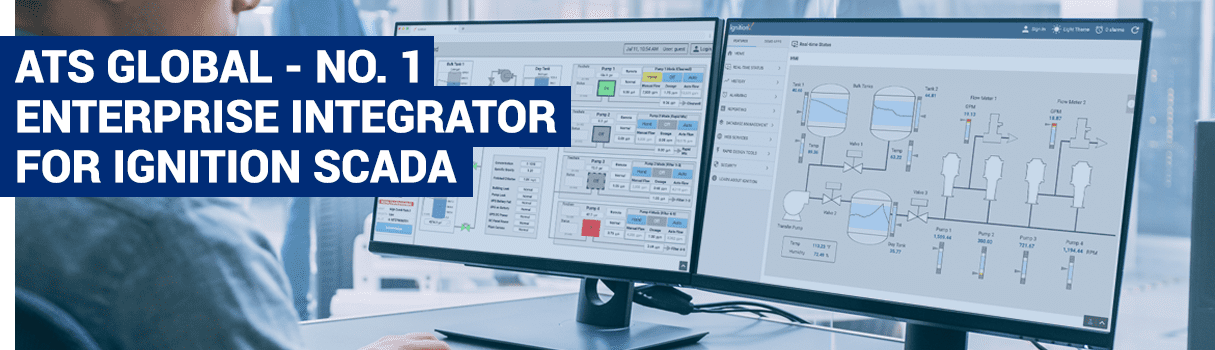
Up to now libraries for bottling and packaging plants (WS Pack) and machines for food processing (WS Food) have been realized.”Ĭommunication via a plug-and-play principle is made possible by automated parameterization via a device description file. Data points and contents were defined for individual industrial sectors. They also define the data which must be provided for acquisition. Per the Weihenstephan Standards website: “The Weihenstephan Standards (WS) define a universal communication interface for the connecting machines to higher ranking data acquisition systems or MES (Manufacturing Execution systems). Additionally, WS supports the ISA TR88.00.02’s (OMAC PackML) mode manager and state model. WS consists of standardized data using WS production data and the WS communication protocol (WS-proprietary commands used with the TCP/IP protocol). Sidebar: Weihenstephan Standards define communications between machines and MESĭating back to 1999 and founded and developed by the Technical University of Munich (TUM), Chair of Food Packaging Technology, the Weihenstephan Standards (WS) are popular in the beverage filling & packaging industry (WS Pack), and increasingly in the food processing industry (WS Food), and provides the link between the production management level and the machine level. And cybersecurity is as good as your bank’s. With these improvements, machine safety has been evolving from hardwired switches and separate safety controllers to integrated safety systems. It turns out that several improvements in technology have been occurring at every level, including faster processors, cheaper and more dense memory and industry-standard machine programming and communications protocols. Futuristic? Not really-it’s available right now.įE talked with machine builders, system integrators (SIs) and component suppliers to get a handle on what food and beverage processors can expect with the latest and future generations of machine controls. Back at headquarters, senior staff has been following the event, and immediately knows the impact on production and can adjust accordingly. If that’s not possible, your machine builder can log onto the machine and find the fault within minutes-no travel time and no expenses.
#Inductive automation ignition preferred web service how to
When something breaks, chances are the machine can tell you exactly where the problem is and how to fix it.
#Inductive automation ignition preferred web service plus
Today, machine builders are creating hardware and software that communicate with the rest of your plant equipment plus your shop floor MES and ERP systems.


